In the fast-paced world of manufacturing, the concept of Industry 5.0 is becoming increasingly popular, aiming to combine the best of humans and robots through collaboration. While humans remain essential resources for manufacturing systems, they are constantly affected by a number of factors, such as work intensity, skill level and physical conditions, which can lead to an increased risk of work-related injury.
As Industry 5.0 gets closer, collaborative robots are playing a pivotal role in the manufacturing industry as it seeks to enhance the flexibility and responsiveness of production processes. This is where the key to the future lies: in the seamless bridging of the gap between man and machine.
Introduction
Researchers from the Sungkyunkwan University in Suwon, South Korea, proposed a framework to improve human-robot interaction and increase safety and accessibility in manufacturing (full research). They used the TESLASUIT’s motion capture and haptic feedback systems to detect the distance between the human and the robot and to alert the human to potential hazards.
Proposed framework
The proposed framework includes several modules (Figure 1). An operator wears a full-body haptic suit, which is connected to a virtual human via a wireless network. The operator’s movements are mirrored in the virtual world, and collision detection with the robot is tested based on defined assembly sequences. A virtual fence is installed in the robot joint and end effector to prevent accidents during collaborations.
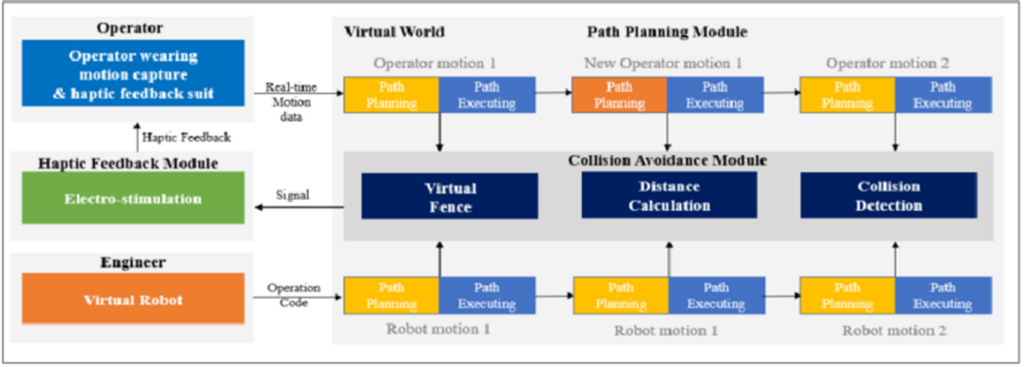
When an accident occurs in the virtual world, the user feels a haptic feedback response to their actions through electrostimulation. If a virtual body part collides with a virtual object, the commutation unit sends pulses from a pulse generator to electrodes in the same vicinity on the wearer’s real body. TESLASUIT uses two types of electrostimulation: TENS and EMS, both of which can be effective in preventing accidents.
The framework also calculates the distance between the human and the robot in real time for seamless interaction. The movement of the robot or real human is first corrected to avoid a collision. The movement is then executed if it is deemed safe. During validation, the real-time distance and a warning message are displayed on the dashboard (Figure 2).
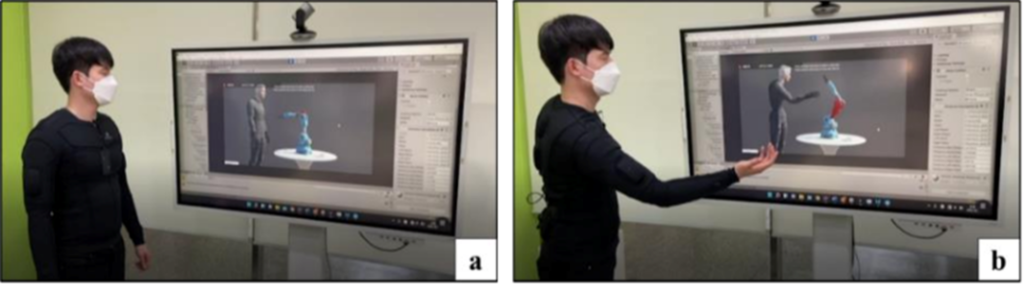
Figure 2. Visualisation of the framework application. The robot
responds when an operator collides with the virtual fence
In the virtual world, a warning message is generated on the dashboard when either a robot or an operator approaches within a certain distance. The haptic feedback is delivered simultaneously to the actual area in the physical world. The operator can detect an abnormal situation while interacting with the robot.
Implementation
The proposed framework is implemented in a virtual testbed with an assembly process for the production of fan filter units. A worker in the vicinity of the manufacturing work-centre is connected by a conveyor line. This work-centre is a typical example of an assembly process where equipment is picked and tasks are performed using the upper body in a fixed position. The basic assembly processes for the product in this virtual testbed are screwing and bolting.
This virtual factory is a real floor-shop-like environment. The aim of the experimental setup is to validate the functionalities when an operator collides with the robot during production.
The virtual fence created, together with the haptic feedback, can help the supervisor monitor real-time data, such as distance calculations and collision counts, displayed on the dashboard. In addition, the current order information is displayed while the human and robot are performing the task. During production hours, the operator and robot should perform a defined movement, after having been tested in the validation process. If an operator fails to maintain the safety distance, a collision is detected and the collision area is highlighted in red and displayed in the skeleton figure.
Conclusion
The research conducted at Sungkyunkwan University in the virtual testbed demonstrates the feasibility of implementing the safety enhancement framework in a real manufacturing environment. By advancing this technology, the TESLASUIT aims to revolutionise the Industry 5.0 manufacturing concept, which will lead to better performance and increased operator satisfaction.
Creating an innovative framework for human-robot interaction using TESLASUIT is a significant step towards human-robot collaboration in the manufacturing industry. Using motion capture and haptic technology, the TESLASUIT could bring human safety, real-time distance measurement and collision avoidance to manufacturing.